
Engine Production Testing
-
For Complete or Replacement content level engines to ensure performance meets specification.
All Complete or Replacement level engines are 100% dyno tested prior to shipment
Includes dynamic engine performance parameters
Run engine 25 minutes at key perfomance points
Record performance curve increments of 100 rpm from low to high idle at conclusion
Test results are logged and archived by serial number for future reference
Performance Results
Turbo Boost Pressure
Engine Horsepower
Exhaust Temperature
Engine Torque
Fuel Burn Rate
Oil Pressure
Crankcase Pressure (High Idle & No Load)
Oil Analysis (Before & After Test)
-
For Long Block or Basic content level engines to ensure performance meets specification
All Long Block or Basic level engines are 100% spin tested prior to shipment
Process
Verification of proper pumping and ensure no frictional losses
Test results are logged and archived by serial number for future reference
Performance Result
Oil Pressure
Oil Analysis (Before & After Test)
-
Check for Fuel Dilution and Coolant Contamination
Check for Bearing Wear
Elemental analysis for wear components using in-house mass spectrometry
-
Ensures part cleanliness
-
Check for external cracks or leaks
Component is magnetized
Apply Magnaglo® Fluorescent solution to its surface
Ultraviolet or “black” light utilized to reveal the smallest surface flaw
-
Check for internal cracks or leaks of all fluid jackets
Block off all engine openings
Pressurize the engine to detect any leaks

“Five Major” Engine Components Testing
-
Inspected for cracks
Milled to ensure flatness
Valve seats & guides machined with precision equipment
9 Point Check:
Magnetic particle crack inspection
Flatness
Leaks
Thickness
Surface Finish
Valve Guides
Valve Recession
Valve seat run-out
Valve face to seat contact
-
Machined with state-of-the-art Rottler F79 Computer Numerical Control (CNC)
Ensure all bores meet exacting dimensional specifications
Honed with latest technology from Sunnen
Wet sleeve engine sleeves are replaced with 100% new sleeves
7 Point Check:
Magnetic particle crack inspection
Flatness
Leaks
Crank bore alignment
Cam bore alignment
Deck height
Counter bores
-
Checked for straightness
Crank & piston pin bores are checked for size
100% new bearings and bushings installed
4 Point Check:
Straightness
Crank bore size
Piston bore size
Center to center dimension
-
Dimensionally & structurally inspected
Ground and micro-polished to exacting tolerances
7 Point Check:
Magnetic particle crack inspection
Rod & main journal diameter
Thrust width
Nose diameter
Rear seal diameter
Bend
Surface finish
-
Examined & straightened
Main journals & lobes checked
Machined to ensure proper valve lift & timing
10 Point Check:
Journal diameter
Journal taper
Out-of-round
Surface finish
Lobe hardness
Lobe lift
Lobe Taper
Bend
Run-out
Intake & exhaust base circle run-out
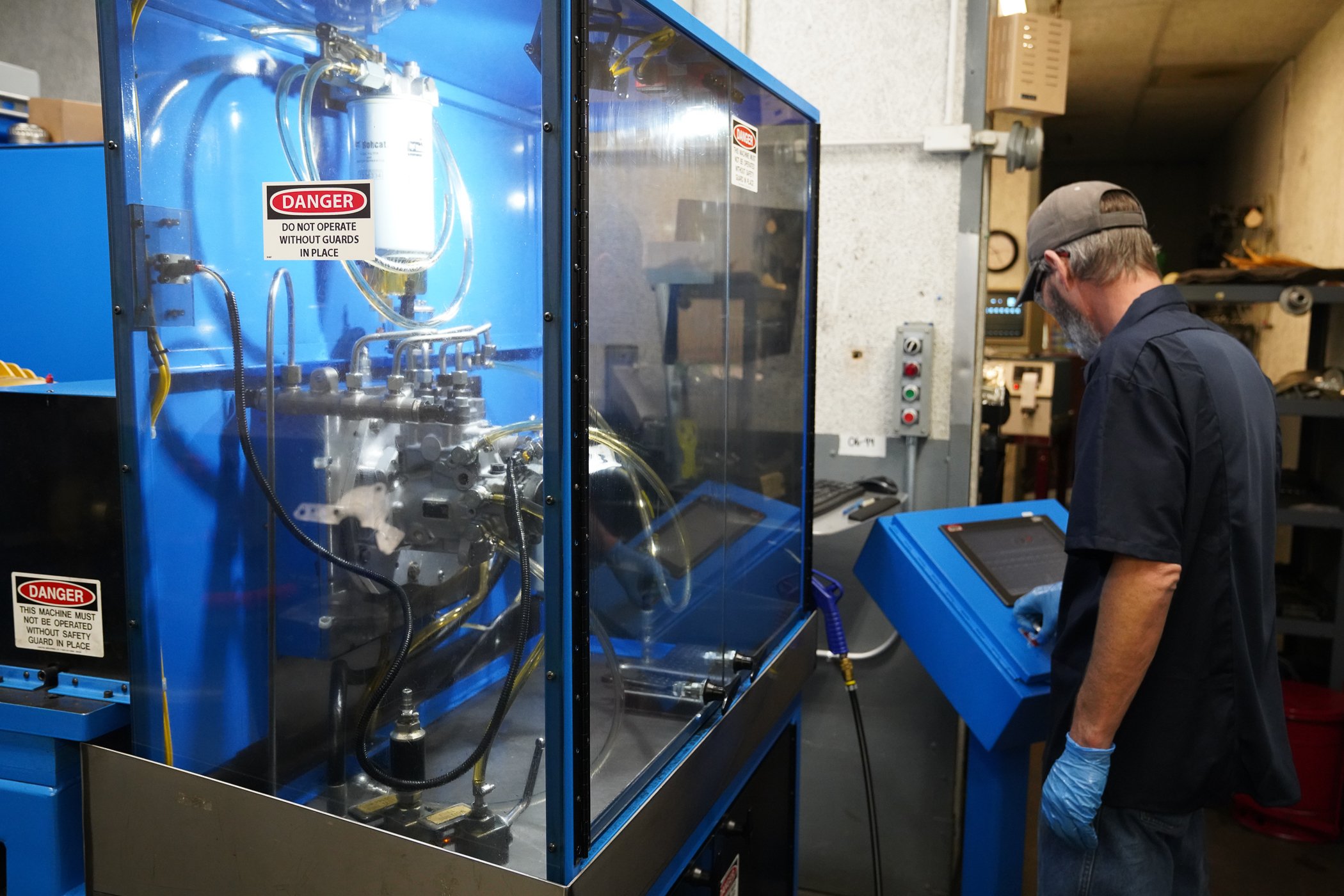
Fuel System Production Testing
-
For both High Pressure Oil & Common Rail Fuel Pumps
Tests both Oil pumps & Fuel Pumps simultaneously if applicable
“HPOP” Test System
Tests up to 50,000 psi or 3,450 bar
Ensures pressure & cubic centimeters (cc) flow requirements under controlled duty cycles
Low idle
Cranking at stated RPM
Rated Horsepower
-
For both Rotary and In-Line Pumps
Checks balance of cylinder flow at a given pressure
-
For both Single & 2-Stage Injectors
Hartridge Fuel Equipment
Measures “pop-off” or pressure to open the nozzle
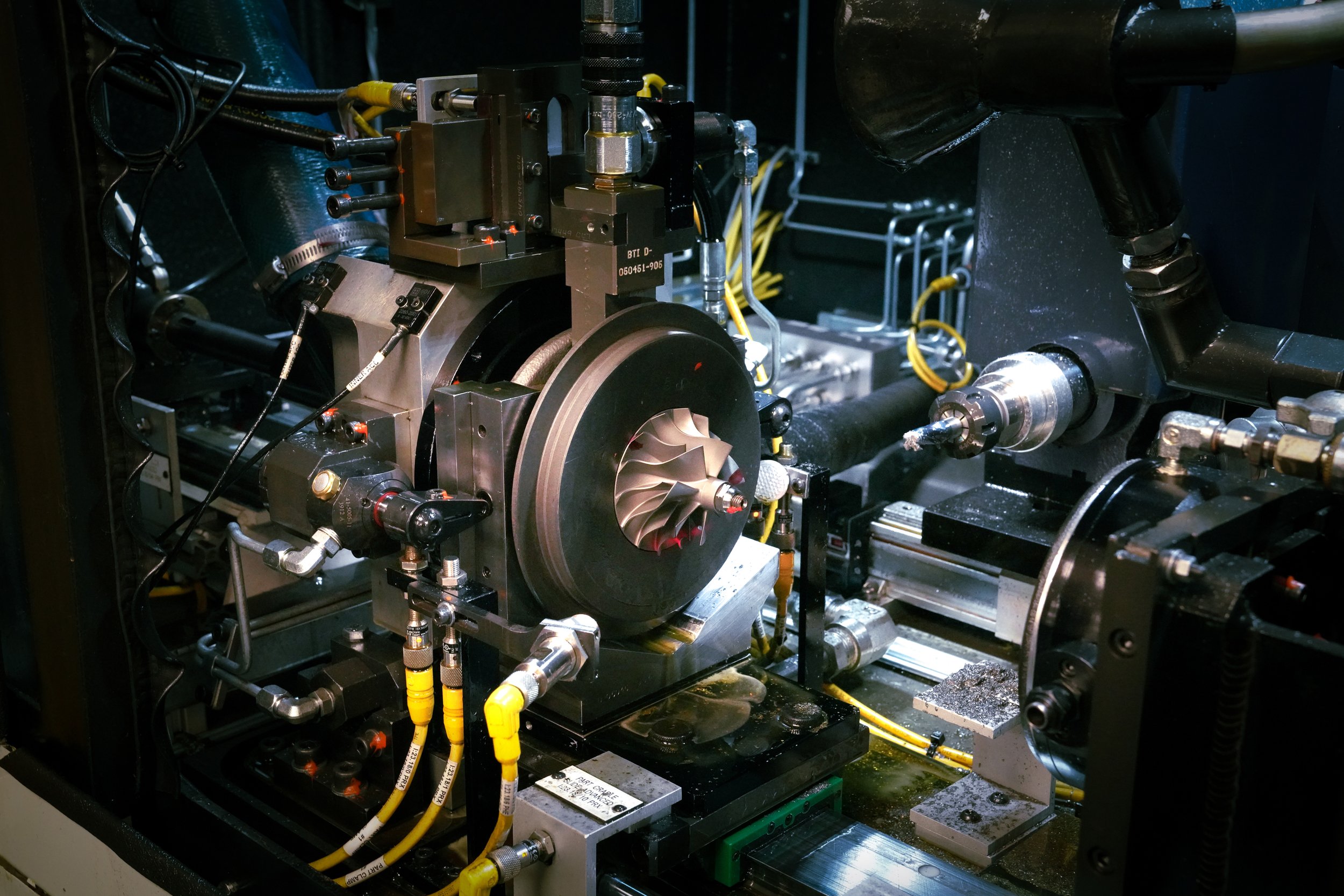
Turbocharger Production Testing
-
To ensure optimal bearing life, reduced noise & vibration
Automated BTI Correction Equipment
All turbochargers are 100% cartridge balanced
Dynamic balance up to 150,000 rpm
Balanced to exceed OEM specifications
-
To ensure optimal bearing life
BTI & Hoffman Equipment
Turbocharger parts are 100% component balanced
Dynamic balance up to 2,500 rpm
Balanced to exceed OEM specifications
-
Check of bearing housing and turbine shafts
Run-out
Surface finish
Cylindricity
-
Ensures proper function of actuators
Used on variable geometry turbochargers